- The materials and the construction method, applied for the first time in the world, reduce the duration of the construction phase by almost 50% and avoid 20% of pollutants.
- The hoisting of the 32-meter-high structure was completed in less than three hours.
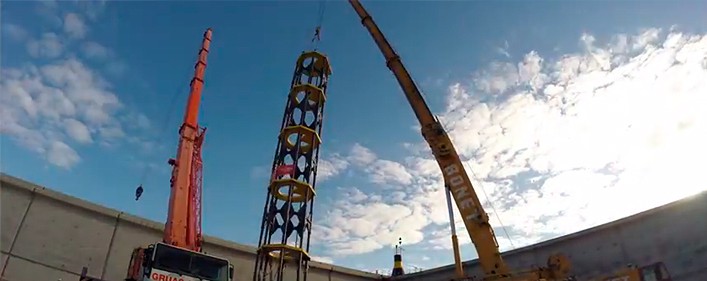
ACCIONA and the Port Authority of Valencia have completed the hoisting of the city’s new lighthouse, the first in the world made from composite materials. The maneuver involved placing the new 32-meter-high lighthouse on its definitive site, the northern extension of the Port of Valencia. It is made from composites that provide higher resistance to exposure to the marine environment, reduce maintenance work and restrict the impact on the environment to a minimum.
The light weight of the composite materials, specifically developed by ACCIONA Infraestructuras’ R&D center, make the construction process of the lighthouse a pioneering one worldwide, with the structure being manufactured in ACCIONA’s Assembly Center in Noblejas (Toledo province). It was transported to Valencia by road, and once in the port was hoisted and anchored on its definitive site, reducing the time of the construction phase and avoiding around 20 per cent of the pollution associated with the construction of these infrastructures using traditional methods. The hoisting of the structure was successfully completed on Friday February 13th and took less than three hours, reducing interference with port operations to a minimum in the process.
Other work will continue following the hoisting of the structure, for example, placing the lamp, The installation is likely to be completed in April.
The new lighthouse, designed by Ignacio Pascual, Director de Infrastructures of the Port Authority of Valencia and developed and produced by ACCIONA Infraestructuras, is innovative in terms of its greater energy self-sufficiency, as it will have ten south-facing solar panels and a vertical axis wind generator that will reduce the energy consumption of the structure considerably. The lighthouse has also been equipped with LED technology, giving a range of 25 nautical miles and an electricity consumption of 70 watts.
Building of the first lighthouse in the world made from composites.
Advantages
The use of composites in the construction of the lighthouse helps to make this kind of infrastructure more sustainable, both in environmental and economic terms.
- Quicker completion of construction work: the total manufacturing and installation time of the lighthouse is 40% lower than with the traditional process.
- Lower impact on port operations: apart from the fact that the total time of building the lighthouse is shorter, the time the port is affected is also much less because the assembly of the structure was done in the factory. This also means a smaller surface area and a shorter occupation time in the port, and less waste and noise in comparison with the work normally involved in the construction of a lighthouse.
- Longer working life of the lighthouse: one of the main advantage of using fiber glass or carbon fiber composites in harsh environmental conditions is that they are not affected by corrosion. This makes them very attractive for use in damp or marine environments; lighthouses built with traditional materials usually suffer considerable degradation, which leads to a shorter working life.
- Reduction in construction and maintenance costs: the use of composites is more efficient in economic terms because the construction process is faster and there is less need for the transport of materials. Furthermore, by resisting environmental conditions better, the lighthouse does not require investments in maintenance.
- A reduction of CO2 emissions in the construction process, due to fewer transfers of heavy materials and a lower level of extraction of aggregates. The environmental impact is believed to be 20% lower when using composites instead of traditional materials.
Related news: Into the future with composites